Shot Blasting Techniques to Boost Industrial Efficiency and Quality
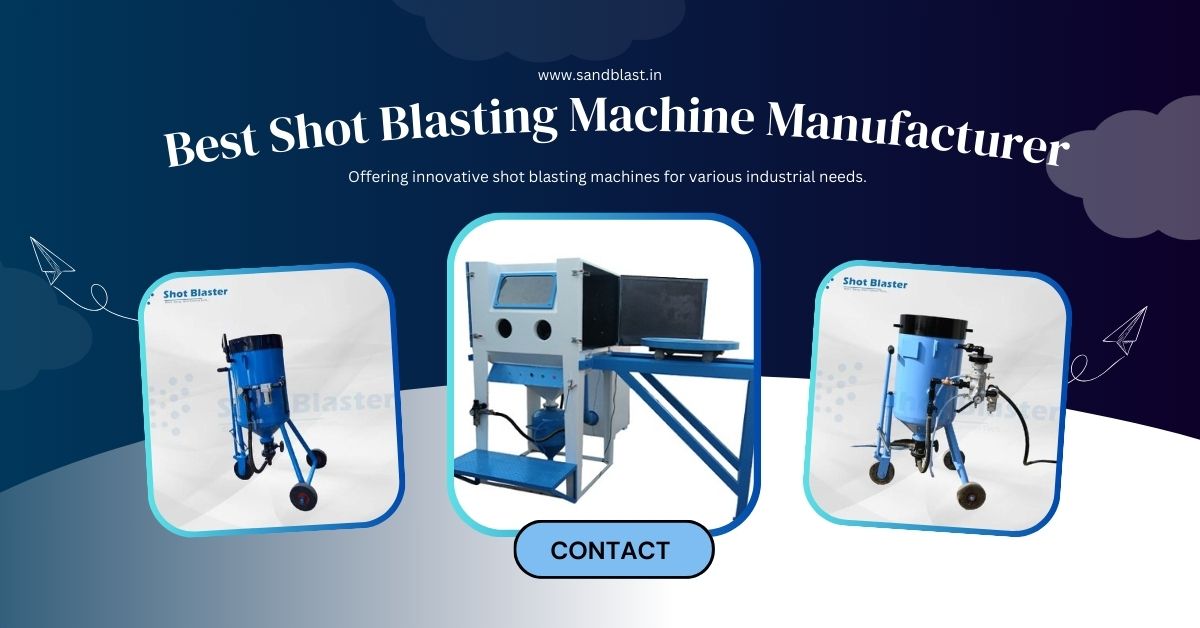
Shot blasting serves as an effective surface preparation technique that employs high-speed abrasive materials to clean and enhance metal surfaces. Unlike sandblasting, which relies on a different mechanism, shot blasting uses a wheel blast system that optimizes its performance on resilient materials. It is widely utilized for tasks like rust removal and improving the adhesion of coatings.
Various industries, including automotive and aerospace, benefit from the efficiency and quality improvements that shot blasting provides. This article examines different shot blasting methods and their advantages for industrial applications.
Understanding Shot Blasting Techniques
Shot blasting techniques focus on surface preparation methods that vary based on the workpiece and desired outcome. Common types include portable shot blasting machines and hanger-type systems, where a centrifugal wheel propels metal shot or other abrasive materials to remove imperfections like rust, mill scale, and cosmetic damage from hard substances.
When comparing efficiency, abrasive blasting is often more effective than sandblasting for tough materials due to the high velocity achieved, making it suitable for industries such as foundry work, automotive, and welding. The choice of abrasives, such as copper, aluminum oxide, or various mesh sizes, influences effectiveness, impacting how well surfaces are cleaned and polished. Factors like hardness, shape, and density of the abrasives are important for the project's success. For softer metals or ceramics, care is needed to avoid damage, while for harder materials, a more intense approach can ensure clean surfaces ready for coatings.
Understanding these principles helps guide the selection of techniques for specific industrial applications.
Benefits of Shot Blasting for Industries
Shot blasting offers numerous benefits for surface preparation and quality enhancement across different industrial applications. This method enhances metal surfaces by eliminating imperfections, mill scale, and debris, resulting in clean surfaces that are ready for coatings or welding.
By employing high-velocity abrasive materials like metal shot, workers can achieve smoother finishes through processes like deburring and polishing, which are important in sectors such as foundry work and automotive manufacturing. According to Shot Blaster, The efficiency of shot blasting, particularly with portable machines and centrifugal wheels, can lead to significant cost savings. It reduces reliance on harsh chemicals often used in sandblasting and enables continuous processes that optimize production. Furthermore, shot blasting supports environmental considerations by minimizing waste through the recycling of abrasive materials.
Unlike conventional methods that may damage softer metals like copper and aluminum, shot blasting effectively prepares hard substances without causing cosmetic harm. This method contributes to sustainable practices in industrial operations by consuming less energy and generating fewer harmful emissions, while still providing effective surface preparation through various abrasives customized for specific shapes and sizes.
Different Types of Shot Blasting Techniques
Abrasive Blasting
Abrasive blasting offers several advantages over other surface preparation methods, such as sandblasting. The use of portable shot blasting machines allows for greater flexibility and effectiveness, particularly with hard substances.
For example, shot blasting with metal shot through a centrifugal wheel can efficiently remove imperfections, mill scale, and coatings from a metal surface. The choice of abrasive material, whether it’s aluminum oxide or steel shots, heavily influences the process. Factors like size, shape, hardness, and density determine how well the abrasive can clean surfaces or polish workpieces. In industrial applications, harder abrasives can handle tough jobs without causing cosmetic damage to soft metals like copper. Safety measures are necessary during abrasive blasting operations to protect workers. Implementing blast cabinets helps control debris, and proper ventilation reduces inhalation of harmful particles.
Continuous processes require training workers to follow protocols for using abrasive materials safely. A shot blasting guide can help ensure best practices are maintained throughout the operation.
Wet Blasting
Wet blasting offers several advantages over traditional dry blasting methods. It uses a mixture of water and abrasive materials, such as metal shot or aluminum oxide, which reduces dust and produces cleaner surfaces. This environment-friendly approach helps minimize cosmetic damage to the workpiece, making it ideal for applications like polishing and deburring, where imperfections must be removed without harming softer metals like copper or ceramics.
Wet blasting is particularly effective in industrial applications such as foundry work, welding preparation, and surface preparation methods that require high velocity for removing mill scale from metals. The use of portable shot blasting machines and blast cabinets ensures proper containment, while the size, shape, and hardness of the abrasives can be adjusted to meet specific requirements.
Overall, wet blasting is an effective technique for achieving clean surfaces and preparing metals for coatings while reducing environmental impact through controlled particle emissions.
Additionally, it is suitable for continuous processes, enhancing efficiency and conserving resources during abrasive blasting tasks.
Dustless Blasting
Dustless Blasting offers several advantages over traditional dry blasting methods, particularly in terms of efficiency and dust reduction. By combining water with abrasive materials like metal shot and aluminum oxide, it minimizes airborne particles, resulting in a cleaner work environment. This method is environmentally friendly as it prevents harmful particles from escaping into the air, benefiting health and safety.
The technique excels in surface preparation for various materials, includinghard substances like steel and ceramics, and is effective on softer metals like copper and aluminum, which might be damaged by dry methods. It is especially useful in industrial applications such as deburring, removing mill scale, and surface polishing.
According to Airo Shot Blast, portable shot blasting machines can access confined spaces, making them ideal for projects that require precision and thorough cleaning. The combination of high velocity and controlled abrasives ensures workpieces have clean surfaces suitable for coatings without causing cosmetic damage. Thus, Dustless Blasting proves to be a versatile option for effective and responsible surface preparation.
Key Equipment in Shot Blasting
Shot Blast Machines
Shot blasting machines vary in design, including portable units and hanger systems. Features such as the size and shape of the abrasive material, like metal shot or aluminum oxide, directly influence performance. The hardness and density of these abrasives affect their effectiveness in blasting, particularly for tough materials. A centrifugal wheel propels abrasives at high velocity toward a workpiece, efficiently removing imperfections, mill scale, and cosmetic damage from metals and ceramics.
This improves surface preparation methods, ensuring clean surfaces for better adhesion of coatings, especially prior to welding. When selecting a shot blast machine, it's important to consider the type of abrasive material that matches the workpiece, the mesh size for optimal effectiveness, and the machine's specifications. Factors like continuous processes, efficiency in cleaning surfaces, and the need for deburring are also significant.
A comprehensive shot blasting guide can assist users in choosing the right model for their specific industrial applications, providing insights into the advantages of each machine type.
Abrasives Used in Shot Blasting
Common abrasives employed in shot blasting include metal shot, aluminum oxide, and various ceramic materials. The hardness, shape, size, and density of these abrasives influence the effectiveness of the blasting process. For instance, metal shot is often selected for its ability to deburr and polish hard substances, making it suitable for industrial applications involving metals and building materials.
On the other hand, softer abrasives like aluminum oxide are ideal for delicate workpieces where less impact is necessary.
The choice of abrasive affects not only the surface finish but also the efficiency of the overall shot blasting process. A high-velocity abrasive can quickly remove imperfections, mill scale, and contaminants from metal surfaces, preparing them for coatings or welding. Different mesh sizes allow for versatile applications, helping to achieve specific finishes required for various materials, such as ceramics or soft metals like copper.
Employing diverse abrasives also has environmental implications. Recyclable abrasives, such as those used in portable shot blasting machines, generate less waste compared to expendable materials, helping to minimize the environmental damage caused by abrasive blasting. Furthermore, blast cabinets equipped with air filtration systems reduce airborne particles, enhancing workplace safety during abrasive blasting activities.
Shot Blasting Techniques for Surface Preparation
When selecting the right shot blasting technique for surface preparation, factors like size, shape, hardness, and density of the abrasive are significant.
For example, using a highly abrasive material like metal shot can effectively deburr and remove imperfections from hard substances, while softer materials, such as copper or aluminum oxide, may not endure the high velocity required for tougher metals. Different abrasives affect the efficiency of processes; using a larger mesh size can enhance cleaning speed but may result in cosmetic damage if not carefully chosen.
Common challenges faced during shot blasting include the risk of embedding contaminants and potential damage to delicate surfaces. Using blast cabinets and portable shot blasting machines can reduce dust and improve safety. Continuous processes in industrial applications can gain from using a centrifugal wheel system that propels the abrasive at high velocity, ensuring clean surfaces for subsequent coating or welding.
A comprehensive shot blasting guide provides insights into addressing these challenges, ensuring effective surface preparation methods are applied while preserving the integrity of various materials, including ceramics and building materials.
Enhancing Quality through Shot Blasting
Shot blasting significantly improves the quality of finished products in industries such as automotive, aerospace, and foundry work by effectively preparing metal surfaces. By using high-velocity abrasive materials like metal shot or aluminum oxide, shot blasting and sand blasting machine removes imperfections, rust, mill scale, and other contaminants from workpieces. This results in clean surfaces that are better suited for coatings, enhancing their adhesion and durability.
Various surface preparation methods, including deburring and polishing, are easily achieved through this technique, providing smoother finishes on hard substances. The choice of abrasives—considering factors like size, shape, hardness, and density—also significantly impacts the treatment's effectiveness.
For example, softer materials like copper and ceramics may become damaged if exposed to harsh abrasives, while harder materials benefit greatly. Using equipment like portable shot blasting machines and blast cabinets ensures efficiency and safety. Furthermore, continuous processes help maintain consistent quality during production, demonstrating how shot blasting is an important part of surface preparation. A shot blasting guide can assist in selecting the appropriate methods and materials for specific industrial applications.
Cost-Effectiveness of Shot Blasting Processes
Cost-effectiveness in shot blasting processes depends on various factors, including the type of abrasive material, equipment choices, and maintenance practices. The selection of abrasives, such as metal shot or aluminum oxide, influences performance and cost.
For example, harder and denser abrasives allow for faster removal of imperfections, like mill scale, speeding up surface preparation and reducing time and expenses. Opting for portable shot blasting machines or different blast cabinet designs can also improve efficiency, especially in foundry work or when working with building materials. Proper equipment maintenance, such as on centrifugal wheels, helps avoid cosmetic damage to the workpiece, ensuring smooth operation. This includes regular inspections for wear and tear on mesh sizes or shapes of the abrasives to maintain quality during operation.
A good shot blasting guide can assist operators in balancing abrasive properties, including size and hardness, which affects costs and the effectiveness of surface polishing or preparing metals and ceramics for welding or coatings.
Environmental Considerations in Shot Blasting
To reduce the environmental impact of shot blasting operations, various measures are being implemented. Companies employ portable shot blasting machines and blast cabinets to contain dust and debris, which helps maintain clean surfaces and prevent contamination. The choice of abrasives affects sustainability; opting for metal shot or recyclable abrasives like aluminum oxide minimizes waste compared to expendable materials.
For instance, hard substances can be recycled, whereas softer metals maygenerate more waste. Advances in technology help cut emissions and waste, with centrifugal wheel systems operating continuously, recycling abrasive materials to limit disposal needs.
Additionally, by selecting appropriate abrasive sizes and shapes, industries can enhance surface preparation methods like deburring and polishing, thus reducing the need for water or harsh chemicals. The management of sandblasting or compressed air also aids in limiting the release of airborne particles. With these technical improvements in industrial applications, shot blasting not only improves the quality of metal surfaces but also fosters increased environmental responsibility.
Future Trends in Shot Blasting Techniques
The future of shot blasting techniques may see advancements like portable shot blasting machines that enhance mobility for surface preparation tasks. With growing environmental regulations, there is a push for methods that minimize dust and waste, potentially leading to more efficient blast cabinets with better air filtration systems. Automation and robotics are likely to improve precision and consistency while reducing cosmetic damage during processes such as deburring and polishing.
For example, automated setups may employ a centrifugal wheel to propel abrasive materials like metal shot and aluminum oxide, efficiently removing mill scale and imperfections from workpieces made of hard substances such as copper and various metals.
Additionally, adaptable systems that can adjust abrasive size, shape, and density could optimize operations across various industrial applications, ensuring clean surfaces for coatings and enhancing overall surface preparation methods. This evolution will make operations safer while also providing better performance and versatility for handling soft metals alongside more robust materials in foundry work and welding tasks.
Tips to Enhance Efficiency in Shot Blasting
1. Optimize Abrasive Material
When selecting the right abrasive material for shot blasting applications, factors such as size, shape, hardness, and density of the abrasives must be taken into account. For instance, a metal shot with a specific mesh size may be chosen for its effectiveness in removing mill scale from hard materials like steel. The choice between aluminum oxide and softer materials is significant, as softer metals like copper may sustain cosmetic damage if the incorrect abrasive is selected.
The abrasive material influences the efficiency of the process; high-velocity abrasives can rapidly eliminate imperfections and prepare metal surfaces for welding or coatings. Performance analysis techniques may include comparing results from portable shot blasting machines and blast cabinets that feature a centrifugal wheel system against traditional sandblasting methods using compressed air.
Continuous processes can improve productivity by recycling abrasives to maintain consistent performance in industrial applications. Therefore, understanding specific cleaning requirements and potential effects of different abrasive materials supports effective surface preparation methods. A shot blasting guide can provide insights into the best abrasives for various workpieces, ensuring cleaner surfaces for better adhesion and finishing.
2. Regular Maintenance of Equipment
Regular maintenance of shot blasting equipment is necessary to keep it running smoothly. Operators should include checks of the blast cabinet, ensuring the centrifugal wheel is free of blockages and that the abrasive material, like metal shot or aluminum oxide, is of the correct size and shape. It’s important to inspect components for any wear, such as cracks, which can occur in portable shot blasting machines or hanger type systems.
Signs of wear include unusual vibrations or changes in the sound of the machine during operation. Neglecting maintenance can lead to decreased efficiency, which may create imperfections on workpieces, such as cosmetic damage when cleaning metals or ceramics. If wear goes unaddressed, the performance of abrasive blasting can drop, causing more downtime for repairs and impacting production rates.
In industrial applications, regular checks help prevent issues with coatings that require precise surface preparation, ensuring that each job—whether for welding, deburring, or removing mill scale—is completed effectively and safely, maintaining the quality of the final product.